I've received my CV1800 (with 16 inch impeller) and am now designing the ductwork layout. I'd appreciate any suggestions for how I might improve my proposed layout and have attached screen shots of my Sketchup layout.
My shop is a small basement shop with low ceilings (7' to bottom of floor joists) and has hot water heating pipes running around the perimeter about 9" below the floor joists. I'm also having to work around the furnace, hot water heater and all of that related plumping. Nonetheless, this should provide a good space for a small hand tool woodworking shop with a limited number of machines. The principal machines that I expect to use quite regularly are: Radial Arm Saw (no table saw), bandsaw, drill press and router table. I may someday add a benchtop planer, a lathe, and downdraft table for sanding. My goal is to capture as much dust as possible right at the source and minimize any micro dust particles escaping into the general air which is shared with the rest of the house.
Constraints I must work around are the heating pipes (shown as pink tubes), a water line I am not allowed to re-route (shown as a green tube), and some I-Beams that support the floor joists (the design calls for situating the CV1800 in between those parallel I-Beams with the motor sticking up between the joists). FWIW, the exhaust will be through 8" insulated HVAC flexible duct to the filter stack.
I'm trying to follow Bill Pentz's recommendations of (a) 6" pipe all the way to the machine, (b) a minimum 4 feet run of straight pipe to the cyclone intake, (c) long straight runs of duct with gentle transitions. The 90 degree elbows are all long sweep elbows with 12 inch radius (2X the pipe diameter) which Bill seems to think are good. The transition to the ceiling level main duct line (first Wye) from the straight pipe from the cyclone inlet will be a Fernco flexible coupling. All of the pipe will be 6-inch diameter PVC ASTM 2729 "Sewer and Drain (S&D)". I've chosen to go with the long sweep 90 degree elbows due to space constraints but more importantly due to the hope that the smoother walled surfaces will have less turbulence than double-45s, but I'm certainly no expert on this. I've noted bababrown's research and comments in this thread: http://www.clearvuecyclones.com/foru...bow-suggestion
Thanks for looking and for any suggestions you can share.
Rush
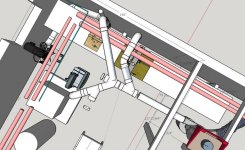
My shop is a small basement shop with low ceilings (7' to bottom of floor joists) and has hot water heating pipes running around the perimeter about 9" below the floor joists. I'm also having to work around the furnace, hot water heater and all of that related plumping. Nonetheless, this should provide a good space for a small hand tool woodworking shop with a limited number of machines. The principal machines that I expect to use quite regularly are: Radial Arm Saw (no table saw), bandsaw, drill press and router table. I may someday add a benchtop planer, a lathe, and downdraft table for sanding. My goal is to capture as much dust as possible right at the source and minimize any micro dust particles escaping into the general air which is shared with the rest of the house.
Constraints I must work around are the heating pipes (shown as pink tubes), a water line I am not allowed to re-route (shown as a green tube), and some I-Beams that support the floor joists (the design calls for situating the CV1800 in between those parallel I-Beams with the motor sticking up between the joists). FWIW, the exhaust will be through 8" insulated HVAC flexible duct to the filter stack.
I'm trying to follow Bill Pentz's recommendations of (a) 6" pipe all the way to the machine, (b) a minimum 4 feet run of straight pipe to the cyclone intake, (c) long straight runs of duct with gentle transitions. The 90 degree elbows are all long sweep elbows with 12 inch radius (2X the pipe diameter) which Bill seems to think are good. The transition to the ceiling level main duct line (first Wye) from the straight pipe from the cyclone inlet will be a Fernco flexible coupling. All of the pipe will be 6-inch diameter PVC ASTM 2729 "Sewer and Drain (S&D)". I've chosen to go with the long sweep 90 degree elbows due to space constraints but more importantly due to the hope that the smoother walled surfaces will have less turbulence than double-45s, but I'm certainly no expert on this. I've noted bababrown's research and comments in this thread: http://www.clearvuecyclones.com/foru...bow-suggestion
Thanks for looking and for any suggestions you can share.
Rush

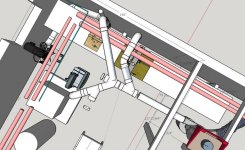
Attachments
Last edited: