AlanBienlein
New member
I want to measure the static pressure ( water column) of my system. Do I install the test tube in the 8" ductwork to test all of my duct runs? Also do I leave it in this location to measure my max static pressure?
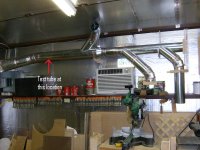
Can I plug this into a formula to give me cfm at my various tools?
I read your supposed to test the blower seperate from the cyclone and then test with no filters but I don't care about big numbers. I just want to know what my system does installed as I would use it. To me those are the numbers that mean anyhting. Any assistance would be appreciated.
Alan
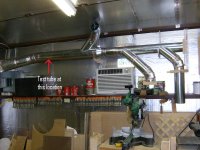
Can I plug this into a formula to give me cfm at my various tools?
I read your supposed to test the blower seperate from the cyclone and then test with no filters but I don't care about big numbers. I just want to know what my system does installed as I would use it. To me those are the numbers that mean anyhting. Any assistance would be appreciated.
Alan